how is wpc board made
Discover the process of creating WPC boards from raw materials to finished product. Learn about the eco-friendly manufacturing techniques and applications.
How is WPC Board Made
The Introduction to WPC Boards
Wood Plastic Composite (WPC) boards have become increasingly popular due to their durability, versatility, and eco-friendliness. These composite materials are a blend of wood fibers or flour and thermoplastic polymers, which can be derived from both virgin and recycled sources. The result is a product that not only mimics the appearance of natural wood but also offers superior resistance to moisture, insects, and rot. This article will delve into the intricate steps involved in the production of WPC boards, including the raw materials used, the machinery involved, and the environmental benefits they bring.
The Production Process of WPC Boards
Mixing of Raw Materials
The first step in creating WPC boards involves the meticulous blending of wood particles with plastic resins. Typically, these materials include sawdust, wood flour, and various types of plastic like polyethylene (PE), polypropylene (PP), or polyvinyl chloride (PVC). The proportions of wood and plastic can vary, but a common ratio might be around 60% wood and 40% plastic. Additives such as UV stabilizers, pigments, and lubricants are often included to enhance the final product’s properties. The mixture is thoroughly blended in large industrial mixers to ensure uniform distribution of all components.
Extrusion Process
Once the raw materials are mixed, the next critical stage is the extrusion process. During this phase, the material is heated and forced through a die that gives it the desired shape, typically a flat sheet or plank. High temperatures are required to soften the plastic matrix so that it can encapsulate the wood fibers effectively. The extruder can be either single-screw or twin-screw, depending on the specific requirements of the production line. Twin-screw extruders are preferred for their ability to provide better mixing and more consistent output.
Pressing and Cooling
After exiting the extruder, the semi-solid material is directed to a calibration unit where it is cooled and shaped. Water baths or vacuum calibrators are commonly used to cool the material rapidly while maintaining its shape. This cooling process is essential to prevent deformation and ensure dimensional stability. Once cooled, the WPC board moves to a cutting station where it is trimmed to the desired length.
Finishing Touches
The final stage involves adding any necessary finishing touches to the WPC board. This may include sanding to achieve a smooth surface, applying a protective coating to enhance weather resistance, or printing designs to mimic natural wood grain. These finishing processes contribute to the aesthetic appeal and longevity of the final product.
Environmental Benefits of WPC Boards
One of the most compelling reasons for choosing WPC boards over traditional wood products is their environmental impact. By using recycled plastics and sustainably sourced wood fibers, WPC boards reduce waste and conserve natural resources. Additionally, the longevity and low maintenance requirements of WPC boards mean they require less frequent replacement, further reducing their overall environmental footprint. Studies have shown that WPC boards can last up to three times longer than conventional wood products, making them a sustainable choice for construction and landscaping projects.
Conclusion
The production of WPC boards is a complex yet fascinating process that combines advanced technology with environmental consciousness. From the initial mixing of raw materials to the final finishing touches, each step plays a crucial role in creating a product that is not only durable and attractive but also environmentally friendly. As awareness of sustainability grows, WPC boards are likely to become even more prevalent in the construction and manufacturing industries.
Reference
Understanding the Properties and Performance of Wood-Plastic Composites: A Comprehensive Review
Choosing the Right Composite Decking Company in Harlem GA
Introduction
When it comes to enhancing your outdoor living space with a composite deck, selecting the right composite decking company in Harlem GA is crucial. The choice you make can significantly impact the longevity, aesthetics, and cost-effectiveness of your project. This article will guide you through the key factors to consider, including warranties, installation processes, and after-sales support, all of which play a vital role in determining the overall value of your composite decking project.
Warranties: Your Assurance of Quality
One of the first things you should look into when choosing a composite decking company in Harlem GA is their warranty offerings. A comprehensive warranty not only ensures that you are investing in a high-quality product but also provides peace of mind knowing that your investment is protected against defects or damage. Companies like Fiberon and Trex often provide warranties that cover both material and workmanship for extended periods, sometimes up to 25 years. Be sure to read the fine print and understand what the warranty covers, as this can greatly affect the long-term value of your deck.
Installation Processes: Professionalism Matters
The installation process is another critical factor to consider. While DIY projects might seem appealing due to potential cost savings, they often come with higher risks of improper installation that can lead to premature wear and tear. Hiring a professional composite decking company in Harlem GA ensures that your deck is installed correctly, adhering to manufacturer guidelines and best practices. Look for companies that employ certified installers who have experience working with specific composite materials. This can be verified by checking their certifications or asking for references from past clients.
After-Sales Support: Ongoing Care
Excellent after-sales support is essential for maintaining the condition of your composite deck over time. Reliable companies in Harlem GA offer customer service hotlines, online chat support, and even regular maintenance tips to help you keep your deck looking its best. Additionally, some companies provide periodic inspections and cleaning services at discounted rates, which can extend the lifespan of your deck. Companies like AZEK and TimberTech are known for their strong customer service and ongoing support, making them popular choices among homeowners.
Conclusion
When selecting a composite decking company in Harlem GA, it’s important to weigh the various factors that contribute to the overall value of your project. From robust warranties to professional installations and excellent after-sales support, each aspect plays a significant role in ensuring that your new composite deck is both beautiful and durable. By carefully considering these elements, you can make an informed decision that will enhance your outdoor living space for years to come.
Reference
Fiberon, Trex, AZEK, TimberTech
Baoding Plastroy WPC Products
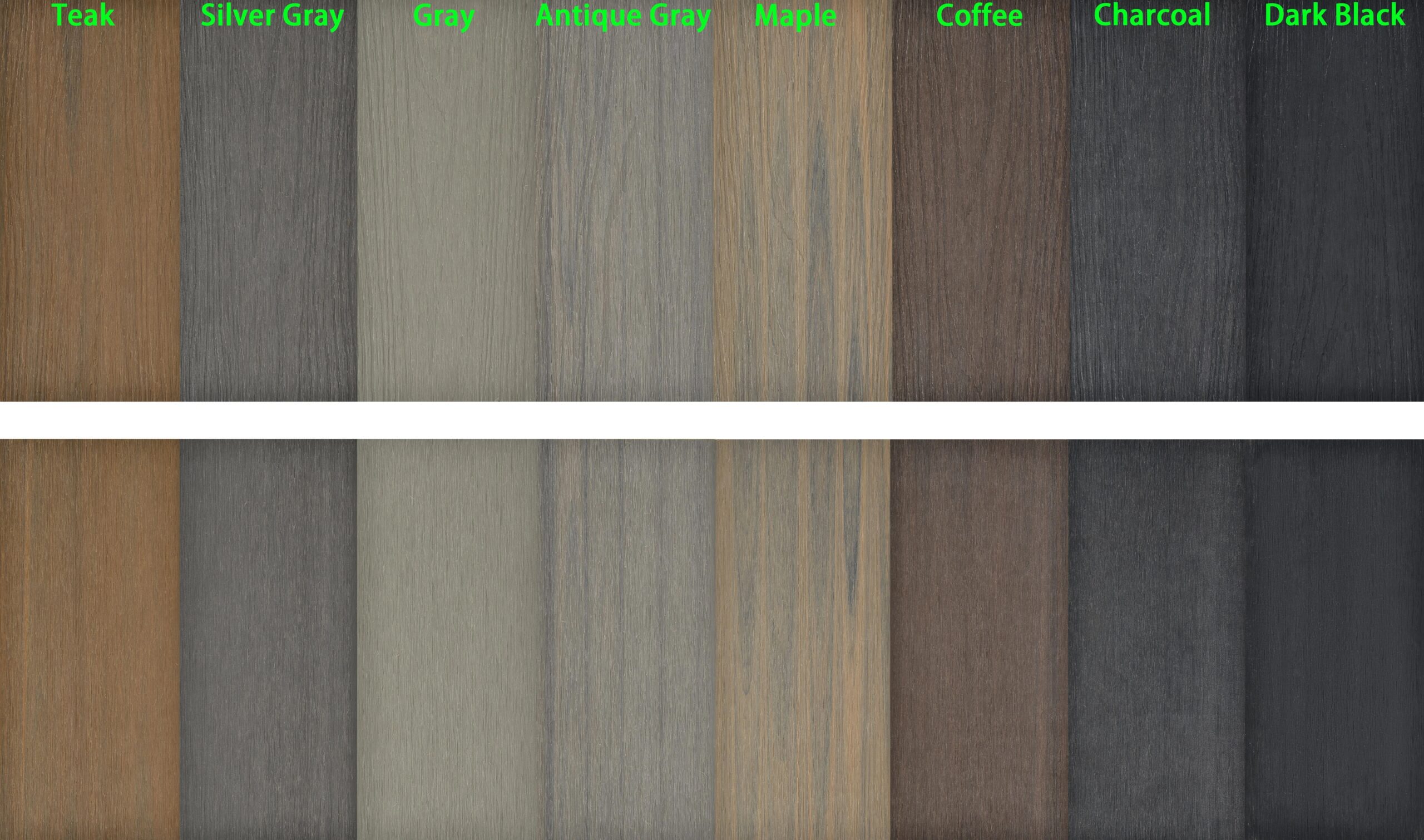
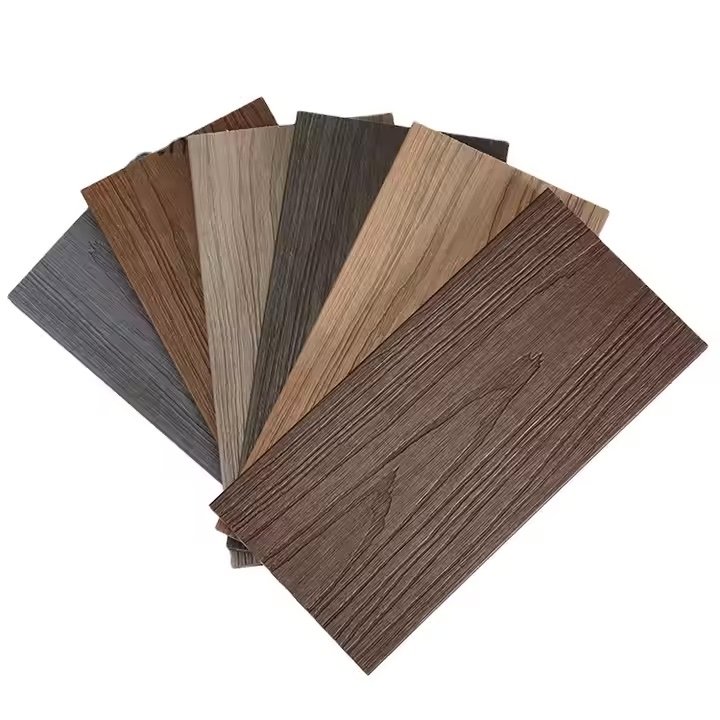
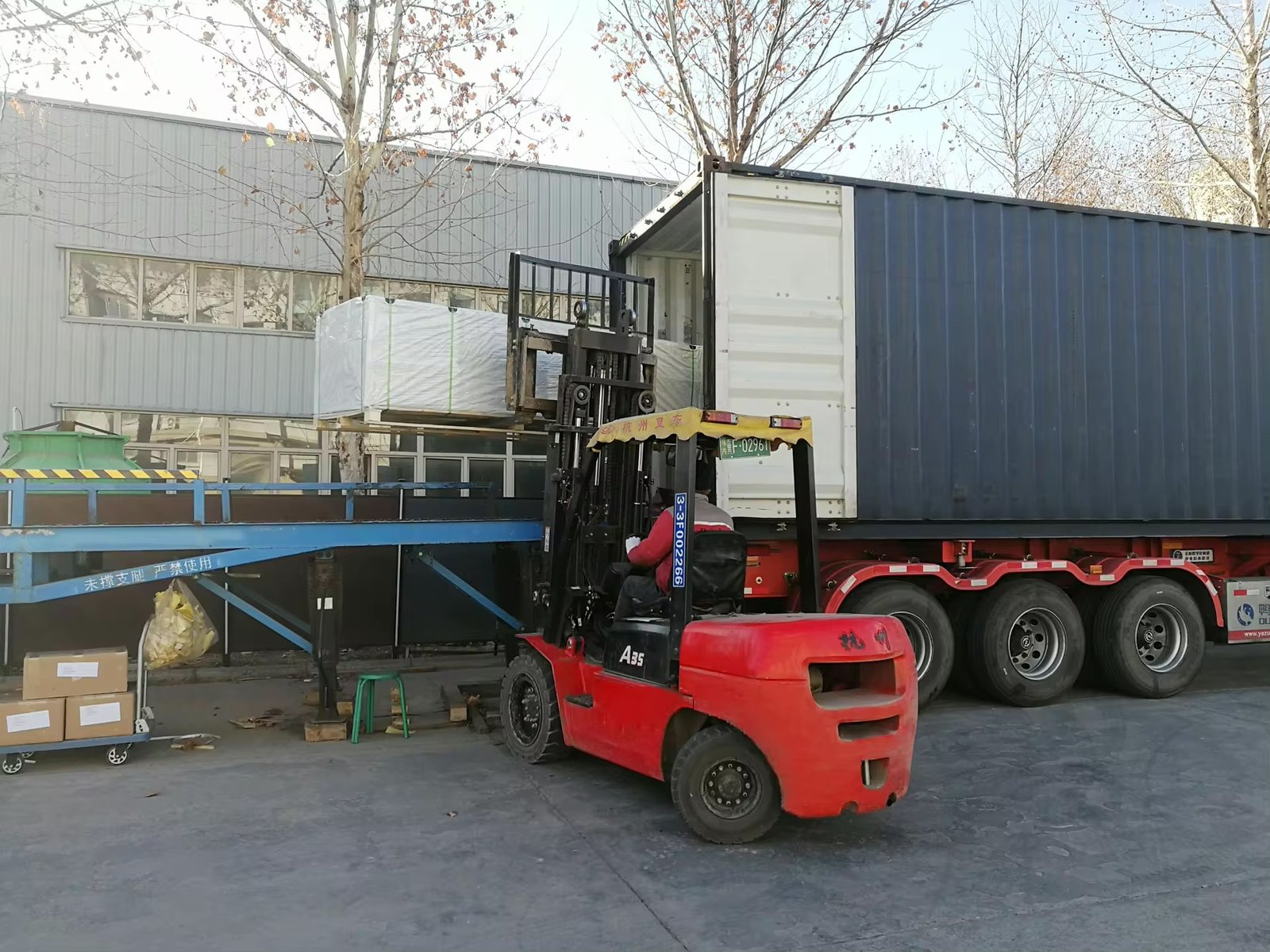
Why Choose Plastory?
Baoding Plastory New Materials Co., Ltd. is a manufacturer of decorative materials with over 9 years of experience and 56 separate production lines.
Currently, our annual production exceeds 30,000 tons, with products exported to more than 50 countries worldwide.
Plastory is the drafting unit of the WPC National Standards and has obtained certifications such as REACH, ASTM, CE, and FSC. Plastory is dedicated to maintaining consistent quality, focusing on details, and prioritizing customer satisfaction.
Our factory is located in Baoding, Hebei Province, China, with a prime location and convenient transportation access. Baoding is approximately a 1.5-hour drive from Beijing Capital International Airport and just 2 hours away from Tianjin Port, making it easy for global clients to visit and facilitating efficient shipping of goods. Our facility spans a large area, equipped with advanced production equipment and modern testing facilities to ensure that every batch of products meets the highest quality standards.
We warmly welcome clients from around the world to visit our factory, where you can see our production processes firsthand and experience our product quality. Please feel free to reach out to us—we are committed to providing you with the best products and services.
Kindly get in touch with us to request a product catalogue.
Reviews
There are no reviews yet.